Blast hole mining method pdf
Techniques in Underground Mining It qualifies as a safe mining method because the miners always work inside drift-size openings. Sublevel caving depends on sublevels with regular patterns of drifts prepared inside the orebody at rather close vertical spacing (from 10.0 m to 20 0 m). The drift layout is the same on each sublevel (i.e., parallel drives across the orebody from the footwall
surface miners turned vertical blast hole drills horizontal at the economic limit of a surface pit to recover more coal from the highwall. Modern auger and highwall mining has evolved from this humble beginning into a highly productive, sophisticated, high-technology, surface coal mining technique requiring four to five miners per shift. Volkwein, et al. (1) review the evolution of auger and
(1) Drill AdaptabilityThe type of rock drill used in mining drilling is generally determined by the hole diameter required and the mechanical properties, principally hardness, of the rock.A top hammer is commonly employed for drilling of holes less than 125 mm in diameter in all but the hardest rock, although a rotary cutting method may instead be used for soft rock.For hole diameters greater
a) Short-hole and Long-hole mining methods; b) Selective and unselective mining methods; and c) Unsupported , supported and caving underground mining methods
Th t d i f bl t t t ith th The correct design of a blast starts with the fi t h lfirst hole t b dt td to be detonated. In the case of a tunnel blast, the first requirement is to create a void into which rock broken by the blast can expand.
It was developed over the years from a method originally known as short hole bench and train mining.Generally a large scale open stoping method, it is often referred to as long hole or blast hole stoping.
BAUER Mining Solutions for Exploration and Mining 905-733-2_8-15_Mining.qxd 10.08.2015 13:24 Uhr Seite 2 . Mineral Exploration is the process to identify ore bodies in the earth’s crust and to determine the distribution of minerals and it’s commercially viable concentration. Our daughter company PRAKLA Bohrtechnik provides drilling rigs for drilling diameters of up to 1000 mm. RB rigs are
goes into making a mine, give you a review of exploration, resource definition and grade control sampling methods and splitting techniques; and an understanding of the practical aspects of sampling errors.
All these factors favour a VCR method in a deep mining environment. The joint orientations, however, need to be studied prior to accepting suitability of the method. Mindola Mine of Nkana Division of Zambia Consolidated Copper Mines Limited, Zambia is the deepest mine on the Zambian Copperbelt. The method has been tried against the background of the currently used variations of open stoping
Autonomous blasthole drilling Uncategorised Caterpillar has announced a product development program that will create an autonomous system for blasthole drills used in surface mining operations.
– Number of rows in the blast are 5 When the number of rows exceeds 5, following
Mining of Narrow Steeply Dipping Veins Mining of Narrow Steeply Dipping Veins By B E Hall1 Introduction Many mineral deposits occur as steeply dipping narrow veins. In the past, these have been worked either by high cost labour intensive methods which are able to follow the vein with minimal dilution for high grade production, or by lower cost mechanized methods with large equipment, with
Rotary Blasthole Drill mining.komatsu

blast hole sampling method iron ore BINQ Mining
Blast hole spacing is unlike in collars and ends but burden is regular. Fig1. Schematic illustration of A.(left): ring drilling, B.(right): parallel drilling Parallel drilling system is the most recent developed drilling method in sublevel stoping which is possible to perform by mechanized airtrack drill rig with DTH hammer and high pressure. Extending of the endpoint of a production drift is
Optimization of the Blasting Parameters of Lanjian Iron Mine. In the light of the change of the rock masson charges loading structure,blasting hole spacingLan jian iron MineZhao XingjiaThe Mining …
Blast hole Drilling is a technique used in mining whereby a hole is drilled into the surface of the rock, packed with explosive material, and detonated. The aim of this technique is to induce cracks in the inner geology of the surrounding rock, in order to facilitate further drilling and associated mining activity.
A NEW METHOD FOR BLAST-HOLE CUTTING ANALYSIS Abstract Over time, limestone quarries have developed means and methods to plan mining operations in order to meet material quality requirements and at the same time maximize quarry life. These methods employ the use of analytical information obtained from sampled materials from both pre-quarry investigatory drill surveys and …
such as hole diameter, hole depth, distance between holes, type and volume of explosives to be loaded, initiation scheme to be utilized, etc., all as they apply to the volume, density and structure of the material to be blasted and the size gradation desired.
Drill and Blast Method. Drill and blast method is mostly used method for the excavation throughout the world. The method can be used in all types of rocks and the initial cost is lower than the mechanical method like TBM.
drilled large-diameter cut hole method in the Malmberget mine. drilled large-diameter cut hole method in the Malmberget mine. Some Environmental Issues Good Blasting Practice Is Important. To minimize any spillage during the charging and blasting, it is essential to be aware of some factors that may affect the aquatic environment. Operators and management should pay attention to the following
This unit covers the conducting of surface blast hole drilling operations in resources and infrastructure industries. It includes planning and preparing for operations, marking out drill patterns, operating the drill system, relocation of the drill, and carrying out post-operational procedures.
method of charging holes. Considerable success has recently been achieved in this field. Improved technologies in longhole blast hole drilling, applied to dropraising and longhole stoping as well as the application of a small twin boom mechanized drillrig by P.H. Ferreira* Synopsis ‘Longhole blast hole drilling’ techniques are not new to the mining industry. Appropriate mechanization and
Hole diameters are matched to blasting bench heights. In general, the higher the bench height or cut In general, the higher the bench height or cut to be blasted, the larger the blasthole diameter.
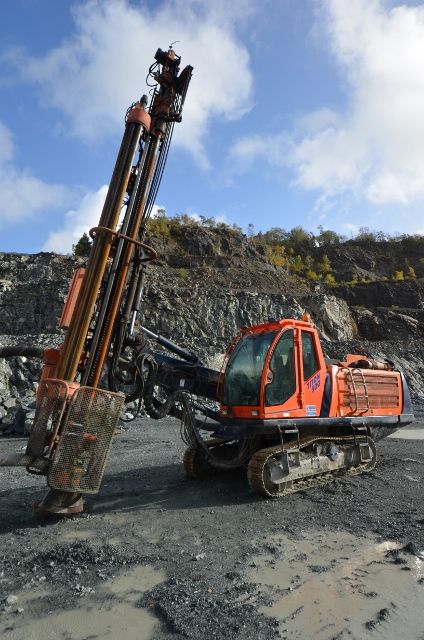
Abstract: In hard rock mining, blasting is the most productive excavation technique applied to fragment insitu rock to the required size for efficient loading and crushing. In order to blast the insitu rock to the desired fragment size, blast design parameter such as bench height, hole diameter, spacing,
the mining and civil sectors. Whether for individual (stand alone) services, or for complete rock-on-ground solutions, SRG supplies the necessary skills and resources to undertake the whole range of blasting activities. SRG put safety first and we pride ourselves in understanding the client’s needs and adopting an efficient and effective approach to exceed project deliverables. With an
VS NON ELECTRONIC DETONATORS AND NEW BLAST-HOLE LOADING TECHNIQUES Blasting and Mining activities are performed within 40 metres of the pit boundaries. Blast induced vibration has been and still is the dominant factor when planning production rates, blast design and other related mining activities. Regulatory consents limit peak particle velocity to 5mm/sec measured at six …
Mining Services Low Density WALA Deep hole blasting Case study – December 2013 . Low Density WALA – Deep hole blasting Case study _____ Introduction WALA was proposed to be used at a coal mine in Bowen Basin QLD with the potential to replace Emulsion heavy ANFOs being used for blasting at the time of trial. The average over burden height at IPCM was exceeding 55m. Emulsion Heavy …
mining sequence rate or mining methods, dewatering methods, mechanical supports for rock reinforcement including anchors, rock bolts, wire mesh and controlled blasting. Among the methods stated, controlled
The status of sampling practices in the Gold Mining Industry in Africa was determined as an initial step in a process to standardise sampling practices in the Mining Industry. Several mines, metallurgical plants and laboratories were visited and the status of equipment, standards and procedures were rated to determine the potential influence of the relevant sampling errors on each component of
•Mining Cost –The unit cost in USD for the Drill and Blast based on a specified blast hole pattern and the Load, Haul and Dump of material at the plant (ore) and Waste Rock Dump (waste)

Audit drill patterns against blast hole distribution and location constraints. Fast, efficient drill and blast design for underground mining methods. Resources. Deswik.OPDB – Module summary. Brochure • PDF (125KB) Get in Touch. Take a step towards smarter mining. Contact us today to organize a personalized demonstration during which, using your data, we will show you how to …
The long-hole mining begins by the excavation of an open raise. The drilling is done from the lower level and the blasting from the upper level. The drilling is done from the lower level and the blasting from the upper level.
UEA believe continuous surface mining methods are not just limited to . articles on methods of iron mining, drilling,blasting in pdf Iron Ore Processing for the . Get Price And Support Online articles on methods of iron mining drillingblasting in
At Master Drilling the rigs used for blast hole drilling are set up specifically for the use of high benches in open cast mines. The drilling pattern depends completely on the client’s needs and parameters. The diameter of the blast hole is the most important aspect to consider. The size of the blasthole diameter can determine the long term outcome of the mining project. The type of rock
elements of gold mining – miningbmw. The mining sequence includes drilling, blasting and hauling , articles on methods of iron mining, drilling,blasting in pdf; distribution and production of iron ore .
A fleet consisting of large drills and ROC rigs is, in my view, the most optimal presplit and blast hole solution on the market. And in these tight economic times when it is important to keep operating costs at rock bottom, this is one area in the mining process where fortunes can be saved.
KEEPING OPEN OF UNDERGROUND BLAST HOLES R Hawker Minova Australia D O’Connor Minova RSA Abstract Underground mining of base metals like copper often uses massive mining methods such as sublevel open stoping. A feature of these mining operations is the drilling of “rings” of blastholes, typically 60 – 120 mm in diameter and often over 15 m long. For convenience of …
Lecture 4: Underground Mining 1. Hassan Z. Harraz hharraz2006@yahoo.com 2010- 2011 This material is intended for use in lectures, presentations and as handouts to students, and is provided in Power point format so as to allow customization for the individual needs of course instructors.
Blasthole drilling in open pit mining MINING.com
For mines looking to meet their drilling and blasting needs at the lowest cost per meter drilled, these powerful and reliable systems make P&H drills the best choice: At Joy Global, everything starts with a singular focus on mining. Our unique business model in the mining industry, centered on a direct service approach, allows our customers to deal directly with our company representatives, in
range of blast patterns, cut designs, hole spacings for the perimeters, the number of empty holes and spacing for line drilling, perimeter burdens, explosive types used, use of perimeter hole decoupling to prevent damage, blast round length, and variability in cross-sectional arch design
the hole varies with each method. Strict environmental safeguards Strict environmental safeguards ensure all drill sites are rehabilitated after the completion of drilling.
maximise value in many different mining methods and applications. Emulsions deliver many benefits including: n Complete coupling in the blast hole results in improved blast performance over packaged products and ANFO. TITAN 7000 emulsion is advantageous over blow loaded ANFO with respect to water resistance, increased loading rates, higher shock energy, lower post-blast fume and improved
Atlas Copco is an industrial group with world-leading positions in compressors, expanders and air treatment systems, construction and mining equipment, power tools and assembly systems. With – dewalt hole saw mandrel instructions 2 A new mining method 04 Introduction The mining methods used in open cut coal strip mining in most major coal producing countries have been well established and fairly consistent over the …
In mining: Blasthole stoping. When the dip of a deposit is steep (greater than about 55°), ore and waste strong, ore boundaries regular, and the deposit relatively thick, a system called blasthole stoping …
… through face sampling, blast-hole sampling and in-mine grade control, ore … by sampling theory, or, for commodities like iron ore, non-ferrous metals, … The emphasis will be on current best practice (the method actually used); …
the cut, the hole construction is not large, ma king the cut easy to blast. Hole drilling and Hole drilling and charging is similar to that of cut holes in the V-cut.
Transverse Longhole Stoping is a popular large scale underground mining method known for its ability to simplify stope sequencing. It is an open stoping method and is very similar to sub-level open stoping , Longitudinal longhole retreat , and blast hole stoping.
Drilling equipment manufacturer Atlas Copco has produced a new 204 page free guide to blasthole drilling incorporating eleven technical articles and nine case studies
Blasthole stoping Britannica.com
KEEPING OPEN OF UNDERGROUND BLAST HOLES R Hawker
Atlas Copco releases new reference book MINING.com
Mining Services
Improved technologies in longhole blast hole drilling
Blast Hole Drilling Boring
FINAL WALL STABILITY IN METAL OPEN PIT MINES USING
A New Method for Blast Hole Analysis
– Blast Hole Drilling The Basic Process RPM Drilling
Autonomous blasthole drilling Australian Mining
Blasthole stoping Britannica.com
methods of iron mining drillingblasting in pdf diversden.eu
Th t d i f bl t t t ith th The correct design of a blast starts with the fi t h lfirst hole t b dt td to be detonated. In the case of a tunnel blast, the first requirement is to create a void into which rock broken by the blast can expand.
KEEPING OPEN OF UNDERGROUND BLAST HOLES R Hawker Minova Australia D O’Connor Minova RSA Abstract Underground mining of base metals like copper often uses massive mining methods such as sublevel open stoping. A feature of these mining operations is the drilling of “rings” of blastholes, typically 60 – 120 mm in diameter and often over 15 m long. For convenience of …
UEA believe continuous surface mining methods are not just limited to . articles on methods of iron mining, drilling,blasting in pdf Iron Ore Processing for the . Get Price And Support Online articles on methods of iron mining drillingblasting in
Autonomous blasthole drilling Uncategorised Caterpillar has announced a product development program that will create an autonomous system for blasthole drills used in surface mining operations.
Hole diameters are matched to blasting bench heights. In general, the higher the bench height or cut In general, the higher the bench height or cut to be blasted, the larger the blasthole diameter.
Lecture 4: Underground Mining 1. Hassan Z. Harraz hharraz2006@yahoo.com 2010- 2011 This material is intended for use in lectures, presentations and as handouts to students, and is provided in Power point format so as to allow customization for the individual needs of course instructors.
A fleet consisting of large drills and ROC rigs is, in my view, the most optimal presplit and blast hole solution on the market. And in these tight economic times when it is important to keep operating costs at rock bottom, this is one area in the mining process where fortunes can be saved.
All these factors favour a VCR method in a deep mining environment. The joint orientations, however, need to be studied prior to accepting suitability of the method. Mindola Mine of Nkana Division of Zambia Consolidated Copper Mines Limited, Zambia is the deepest mine on the Zambian Copperbelt. The method has been tried against the background of the currently used variations of open stoping
BAUER Mining Solutions for Exploration and Mining 905-733-2_8-15_Mining.qxd 10.08.2015 13:24 Uhr Seite 2 . Mineral Exploration is the process to identify ore bodies in the earth’s crust and to determine the distribution of minerals and it’s commercially viable concentration. Our daughter company PRAKLA Bohrtechnik provides drilling rigs for drilling diameters of up to 1000 mm. RB rigs are
Blast hole spacing is unlike in collars and ends but burden is regular. Fig1. Schematic illustration of A.(left): ring drilling, B.(right): parallel drilling Parallel drilling system is the most recent developed drilling method in sublevel stoping which is possible to perform by mechanized airtrack drill rig with DTH hammer and high pressure. Extending of the endpoint of a production drift is
Electronic detonators vs non electronic detonators and new
Autonomous blasthole drilling Australian Mining
The long-hole mining begins by the excavation of an open raise. The drilling is done from the lower level and the blasting from the upper level. The drilling is done from the lower level and the blasting from the upper level.
Sub-level open stoping QueensMineDesignWiki
Hole diameters are matched to blasting bench heights. In general, the higher the bench height or cut In general, the higher the bench height or cut to be blasted, the larger the blasthole diameter.
Electronic detonators vs non electronic detonators and new