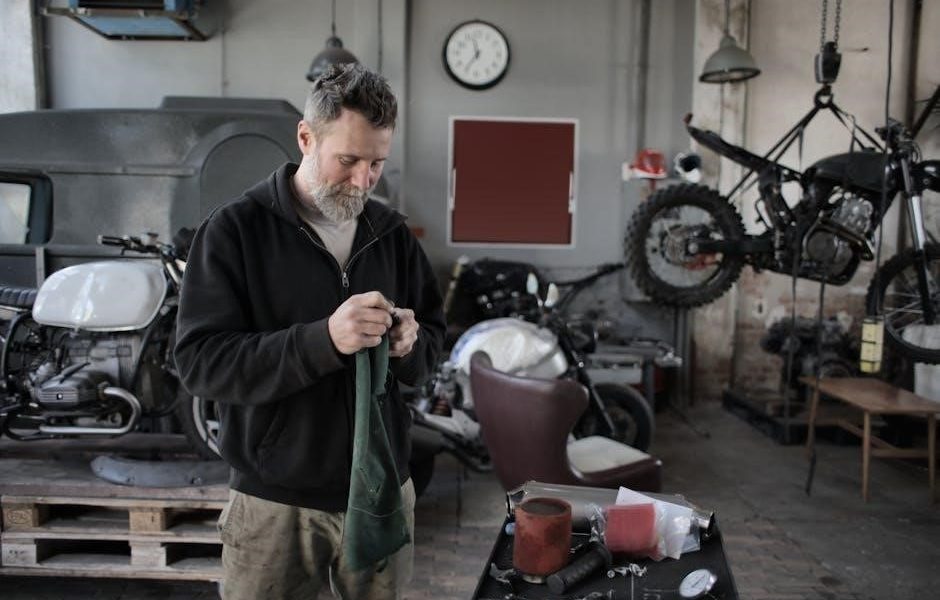
sub zero 650 service manual pdf
The Sub-Zero 650 Service Manual is a comprehensive guide designed for authorized personnel, providing detailed troubleshooting, repair, and maintenance instructions for optimal appliance performance and longevity․
1․1 Overview of Sub-Zero 650 Refrigerator
The Sub-Zero 650 refrigerator is a high-end built-in appliance designed for superior performance and reliability․ Known for its advanced cooling system, it features dual refrigeration technology, maintaining precise temperature and humidity control․ The unit includes a full-extension freezer drawer, magnetic door seals, and a Sabbath mode for energy efficiency․ Its sleek design integrates seamlessly into modern kitchens, offering ample storage and customizable options to suit various culinary needs while ensuring optimal food preservation and freshness․
1․2 Importance of the Service Manual
The Sub-Zero 650 Service Manual is essential for authorized service personnel to diagnose and repair issues efficiently․ It provides detailed diagnostic procedures, schematic diagrams, and parts lists, ensuring accurate troubleshooting and maintenance․ The manual also includes technical specifications, repair guidelines, and safety precautions, making it indispensable for maintaining the appliance’s optimal performance and longevity․ By following the manual, technicians can address common issues like temperature control problems and ice maker malfunctions effectively, preventing further damage and ensuring reliable operation․
Types of Manuals Available for Sub-Zero 650
The Sub-Zero 650 offers various manuals, including User, Service, Installation, Design, and Technical Specifications, each providing specific guidance for operation, maintenance, and repair․
2․1 User Manual
The Sub-Zero 650 User Manual is essential for everyday operation, offering clear instructions on features, settings, and care tips to ensure optimal performance and longevity of the appliance․
2․2 Service Manual
The Sub-Zero 650 Service Manual provides in-depth technical details, diagnostic procedures, and repair guidelines exclusively for authorized service personnel, ensuring proper maintenance and efficient troubleshooting of the refrigerator․
2․3 Installation Manual
The Sub-Zero 650 Installation Manual offers step-by-step instructions for proper unit setup, including leveling, electrical connections, and placement guidelines, ensuring a seamless integration into your kitchen․ Designed for authorized personnel, it provides detailed diagrams and specific requirements to guarantee optimal performance and safety during installation․
2․4 Design Manual
The Sub-Zero 650 Design Manual provides detailed insights into the product’s design, including dimensions, configurations, and styling options․ It serves as a resource for architects, designers, and homeowners to ensure seamless integration into kitchen spaces․ The manual highlights aesthetic features, customization options, and compatibility with various kitchen layouts, helping to achieve a balance between functionality and visual appeal․
2․5 Technical Specifications
The Sub-Zero 650 Technical Specifications outline the product’s operational and physical details, including dimensions, electrical requirements, and cooling system capabilities․ This section provides precise measurements, voltage needs, and performance metrics, ensuring compatibility with various installation environments․ It also details components like compressors, evaporators, and condensers, offering a clear understanding of the appliance’s technical framework for proper installation and maintenance․
Key Features of Sub-Zero 650 Service Manual
The Sub-Zero 650 Service Manual features detailed diagnostic procedures, schematic diagrams, and a comprehensive parts list, aiding in efficient troubleshooting and repairs․
3․1 Detailed Diagnostic Procedures
The Sub-Zero 650 Service Manual includes step-by-step diagnostic procedures, enabling technicians to identify issues efficiently․ These procedures cover common problems such as temperature fluctuations and ice maker malfunctions, guiding through systematic checks and tests․ By following these steps, service personnel can pinpoint faults accurately, ensuring repairs are swift and effective․ Detailed diagnostic flowcharts and error code explanations further enhance the troubleshooting process, making it easier to resolve issues and restore optimal performance․
3․2 Schematic Diagrams and Wiring
The Sub-Zero 650 Service Manual provides detailed schematic diagrams and wiring layouts, essential for understanding the appliance’s electrical system․ These visuals simplify complex circuits, aiding technicians in identifying and resolving electrical issues․ Clear wiring diagrams outline connections between components, while exploded views highlight relationships between parts․ This section is crucial for diagnosing and repairing electrical faults, ensuring safe and accurate servicing․ The manual’s visual guides are indispensable for authorized personnel to maintain the refrigerator’s performance and reliability effectively․
3․3 Parts List and Exploded Views
The Sub-Zero 650 Service Manual includes a comprehensive parts list and exploded views, enabling technicians to identify and source components efficiently․ Detailed diagrams visually break down the refrigerator’s structure, showing how parts interconnect․ This section simplifies ordering replacements and aids in disassembly and reassembly processes․ Accurate part numbers and descriptions ensure precise repairs, while exploded views provide a clear understanding of component locations and relationships, making maintenance and repair tasks more straightforward and effective for authorized service personnel․
3․4 Troubleshooting Guide
The Sub-Zero 650 Service Manual features an extensive troubleshooting guide to help identify and resolve common issues․ It provides step-by-step instructions for diagnosing problems, such as temperature fluctuations or ice maker malfunctions․ The guide includes error codes, possible causes, and detailed solutions, ensuring efficient repairs․ Technicians can quickly pinpoint faulty components and address them using the manual’s clear, systematic approach․ This section is invaluable for authorized personnel, offering practical solutions to restore optimal performance and functionality to the refrigerator․
Technical Specifications of Sub-Zero 650
The Sub-Zero 650 features advanced compressor and condenser systems, efficient evaporator coils, and precise electrical requirements to ensure reliable performance and energy efficiency in refrigeration․
4․1 Compressor and Condenser Details
The Sub-Zero 650 is equipped with a high-efficiency hermetically sealed compressor, designed for quiet operation and reliable performance․ The condenser features advanced coil technology, ensuring optimal heat dissipation and energy efficiency․ These components work in tandem to maintain consistent refrigeration levels, with the compressor providing the necessary pressure to drive the cooling process․ The condenser’s durable construction and efficient design contribute to the unit’s overall reliability and longevity, making it a key element in the appliance’s cooling system․
4․2 Evaporator and Cooling System
The Sub-Zero 650 features a high-efficiency evaporator designed to ensure consistent and precise temperature control․ The evaporator is constructed from durable materials, such as aluminum, to maximize heat transfer and reliability․ The cooling system utilizes a fan to circulate air evenly over the evaporator coils, ensuring optimal performance․ This design minimizes temperature fluctuations and maintains freshness․ Regular maintenance, such as cleaning the evaporator, is essential for sustaining efficiency․ The system also includes defrost mechanisms to prevent ice buildup, ensuring uninterrupted operation and longevity․
4․3 Electrical Requirements
The Sub-Zero 650 requires a dedicated 115V, 60Hz electrical circuit with a minimum of 15 amps․ Proper grounding is essential for safe operation․ The unit should be connected to a circuit protected by a 15- or 20-amp fuse or circuit breaker․ Avoid shared circuits with other high-power appliances to ensure consistent performance․ The electrical connection must comply with local codes and regulations․ Refer to the manual or consult a certified technician for specific wiring and installation requirements to ensure safety and optimal functionality․
Service and Repair Guidelines
The Sub-Zero 650 service manual provides detailed instructions for authorized personnel, ensuring safe and effective repairs․ It includes step-by-step procedures for common issues and complex diagnostics․
5․1 Precautions for Authorized Personnel
Before performing any service or repair on the Sub-Zero 650, authorized personnel must disconnect power and wear appropriate protective gear․ Ensure all safety protocols are followed to avoid injuries or damage․ Use only genuine Sub-Zero parts to maintain warranty validity and performance․ Refer to the manual for specific disassembly and reassembly instructions․ Always follow Sub-Zero’s recommended procedures to ensure safety and effectiveness․ Contact Sub-Zero’s service department for technical assistance if unsure about any procedure․
5․2 Disassembly and Reassembly Instructions
Disassembly and reassembly of the Sub-Zero 650 must be performed carefully to avoid damage․ Start by disconnecting power and removing exterior components like grilles and drawers․ Follow the manual’s step-by-step guide for accessing internal systems․ Use specialized tools for delicate parts․ Reassembly should mirror disassembly, ensuring all components are securely fastened․ Refer to exploded views and parts lists for clarity․ Always use genuine Sub-Zero parts and adhere to torque specifications․ If unsure, consult Sub-Zero’s technical support for assistance․
5․3 Common Repair Scenarios
Common repair scenarios for the Sub-Zero 650 include addressing faulty condenser fan motors, ice maker malfunctions, and evaporator issues․ Start by identifying symptoms like unusual noises or temperature fluctuations․ Consult the manual for diagnostic steps and solutions․ For example, a faulty fan motor may require replacement, while ice maker issues could stem from clogged water filters or faulty sensors․ Always refer to the troubleshooting guide for step-by-step solutions․ If repairs are complex, contact Sub-Zero’s certified service technicians for professional assistance․
Troubleshooting Common Issues
Troubleshooting the Sub-Zero 650 involves identifying symptoms like temperature fluctuations or ice maker malfunctions․ Initiate diagnostic mode by pressing specific keys to locate issues․ Consult the manual for step-by-step solutions and error code interpretations․ Address problems like faulty sensors or clogged filters, and contact certified technicians for complex repairs․
6․1 Temperature Control Problems
Temperature control issues in the Sub-Zero 650 often stem from faulty sensors, blocked vents, or compressor malfunctions․ Check if the condenser is clean and free of obstructions․ Ensure proper door seals to maintain consistent cooling․ If the unit is not cooling, initiate diagnostic mode to identify error codes․ Refer to the service manual for specific troubleshooting steps and repair procedures․ Addressing these issues promptly prevents food spoilage and ensures optimal performance․ Always consult certified technicians for complex repairs․ Regular maintenance can prevent such problems․ Follow the manual’s guidelines for resolving temperature-related faults effectively․ Ensure all electrical connections are secure and functioning properly․ If issues persist, contact Sub-Zero’s customer support for assistance․
6․2 Ice Maker Malfunction
The Sub-Zero 650 ice maker may malfunction due to water supply issues, clogged filters, or electrical faults․ Check the water line for blockages or leaks and ensure the filter is clean․ If the ice maker doesn’t produce ice, verify that it is turned on and properly aligned․ Refer to the troubleshooting guide in the service manual for step-by-step diagnostics; Resetting the ice maker or replacing worn parts may resolve the issue․ If problems persist, contact a certified technician for professional assistance․ Regular maintenance, such as cleaning the ice maker and checking water flow, can prevent future malfunctions․ Ensure all electrical connections are secure and functioning correctly․ Follow the manual’s instructions for disassembling and repairing the ice maker safely․ Always use genuine Sub-Zero replacement parts for optimal performance․ If the issue is related to froze components, thawing may be necessary․ Consult the service manual for detailed repair procedures and guidelines․ Addressing the problem promptly ensures consistent ice production and prevents further damage․ If unsure, seek help from Sub-Zero’s customer support or authorized service providers․ They can provide expert diagnostics and solutions tailored to your unit․ Maintaining your ice maker properly enhances its longevity and efficiency․ Always adhere to safety precautions when performing repairs․ If the ice maker is not functioning after troubleshooting, consider replacing it with a new one․ Keep the ice maker clean to avoid contamination and ensure hygiene․ Follow the manual’s instructions for routine maintenance and repairs․ If the issue is related to the control board, check for error codes and reset the system․ Ensure the ice maker is level and properly installed․ If the problem persists, refer to the technical specifications for further guidance․ Regularly updating your knowledge with the latest service manual ensures you can address issues effectively․ Always prioritize safety when working with electrical components․ If the ice maker is damaged beyond repair, order a replacement part from Sub-Zero’s official distributors․ Ensure the new part is compatible with your model before installation․ Follow the manual’s exploded views for accurate disassembly and reassembly․ If you are not confident in your abilities, it is recommended to hire a professional․ Keep track of maintenance schedules to prevent future malfunctions․ The service manual provides detailed instructions for diagnosing and repairing ice maker issues․ Use the parts list to identify and replace faulty components․ If the ice maker is not producing ice, check the temperature settings and ensure they are within the recommended range․ If the issue is related to the evaporator, refer to the schematic diagrams for guidance․ Ensure all parts are securely fastened after repairs․ If the ice maker is noisy, check for loose components and tighten them as needed․ If the ice maker is leaking, inspect the water supply lines and connections for damage․ If the ice maker is producing too much ice, adjust the settings according to the manual’s instructions․ If the ice maker is not turning off, check the control board for malfunctions․ If the ice maker is frozen, allow it to thaw completely before restarting; If the ice maker is not ejecting ice properly, check the ejector arm for obstructions․ If the ice maker is slow, check the water pressure and filter condition․ If the ice maker is producing small ice cubes, adjust the water level as per the manual․ If the ice maker is not starting, check the power supply and electrical connections․ If the ice maker is making noise, check for worn or damaged parts․ If the ice maker is not aligned properly, adjust it according to the manual’s instructions․ If the ice maker is damaged, replace it with a genuine Sub-Zero part․ If the ice maker is not functioning after repairs, contact a certified technician for further assistance; Always follow the service manual’s guidelines for safe and effective repairs․ If the ice maker is not covered under warranty, purchase a replacement part directly from Sub-Zero or an authorized distributor․ If the ice maker is still under warranty, contact Sub-Zero’s customer service for a replacement․ If the ice maker is not working, check the circuit breaker or fuse for electrical issues․ If the ice maker is not responding to controls, reset the unit or check for software updates․ If the ice maker is not producing clear ice, check the water quality and filter condition․ If the ice maker is not producing enough ice, adjust the production settings as per the manual․ If the ice maker is overproducing ice, reduce the production settings․ If the ice maker is not turning on, check the power button and ensure it is functioning correctly․ If the ice maker is not dispensing ice, check the dispenser chute for blockages․ If the ice maker is not crushing ice properly, check the crusher blades for wear․ If the ice maker is not making ice cubes, check the mold for damage․ If the ice maker is not filling with water, check the water supply valve for proper operation․ If the ice maker is not shutting off, check the float switch for malfunctions․ If the ice maker is not functioning after cleaning, ensure all parts are dry and properly reassembled․ If the ice maker is not producing ice after resetting, check for error codes and address them accordingly․ If the ice maker is not working, refer to the troubleshooting guide in the service manual for detailed solutions․ Always ensure the ice maker is clean and free of debris for optimal performance․ If the ice maker is not functioning, check the user manual for basic troubleshooting steps․ If the ice maker is not producing ice, check the temperature settings and ensure they are set correctly․ If the ice maker is not working, check the electrical connections and ensure they are secure․ If the ice maker is not producing ice, check the water supply and ensure it is turned on․ If the ice maker is not functioning, check the control panel for error messages․ If the ice maker is not working, check the circuit board for any signs of damage․ If the ice maker is not producing ice, check the evaporator coils for frost buildup․ If the ice maker is not functioning, check the drain for blockages and ensure it is clear․ If the ice maker is not working, check the water filter and replace it if necessary․ If the ice maker is not producing ice, check the ice maker switch and ensure it is turned on․ If the ice maker is not functioning, check the wiring for any signs of damage or wear․ If the ice maker is not working, check the thermostat settings and ensure they are within the recommended range․ If the ice maker is not producing ice, check the ice maker module for proper operation․ If the ice maker is not functioning, check the door switches and ensure they are working correctly․ If the ice maker is not working, check the ice maker’s alignment and adjust it if necessary․ If the ice maker is not producing ice, check the ice maker’s water supply line for kinks or blockages․ If the ice maker is not functioning, check the ice maker’s electrical connections and ensure they are secure․ If the ice maker is not working, check the ice maker’s control board for any signs of malfunction․ If the ice maker is not producing ice, check the ice maker’s water inlet valve for proper operation․ If the ice maker is not functioning, check the ice maker’s drain pump for proper operation․ If the ice maker is not working, check the ice maker’s temperature sensor for accuracy․ If the ice maker is not producing ice, check the ice maker’s defrost timer for proper function․ If the ice maker is not functioning, check the ice maker’s compressor for proper operation․ If the ice maker is not working, check the ice maker’s condenser coils for cleanliness and proper airflow․ If the ice maker is not producing ice, check the ice maker’s evaporator fan for proper operation․ If the ice maker is not functioning, check the ice maker’s wiring harness for any signs of damage․ If the ice maker is not working, check the ice maker’s fuses or circuit breakers for any signs of tripping․ If the ice maker is not producing ice, check the ice maker’s water pressure and ensure it is within the recommended range․ If
6․3 Error Codes and Solutions
The Sub-Zero 650 service manual provides detailed error codes and solutions to help diagnose and resolve issues quickly․ Common error codes include E1, E2, and E3, which indicate sensor malfunctions, communication errors, or system faults․ Refer to the troubleshooting guide for step-by-step solutions․ For example, E1 may require checking the temperature sensor or wiring connections․ Resetting the unit or replacing faulty components often resolves the issue․ If error codes persist, contact a certified technician for professional assistance․ Always consult the manual for accurate error code interpretations and repair procedures to ensure optimal performance and prevent further damage․ Regular maintenance can help minimize error occurrences․ If unsure, rely on Sub-Zero’s customer support or authorized service providers for expert guidance․ Addressing error codes promptly ensures your appliance operates efficiently and reliably․ Use genuine parts for replacements to maintain warranty coverage and performance․ If the error code relates to software, updating the system may be necessary․ Follow the manual’s instructions for safe and effective repairs․ If the issue is complex, do not hesitate to seek professional help․ Keep the service manual handy for quick reference․ If the error code indicates a critical system failure, turn off the appliance and contact support immediately․ Always prioritize safety when addressing error codes and performing repairs; If the error code is not listed in the manual, contact Sub-Zero’s technical support for further assistance․ If the error code persists after troubleshooting, replace the faulty component as directed․ If the error code relates to the control board, check for firmware updates or replace the board if necessary․ If the error code indicates a temperature issue, ensure proper ventilation and check the condenser․ If the error code relates to the ice maker, refer to the ice maker troubleshooting section․ If the error code is due to a power failure, reset the unit and monitor its operation․ If the error code indicates a water supply issue, check the water line and filter․ If the error code relates to the evaporator, ensure proper airflow and check for blockages․ If the error code persists after repairs, contact a certified technician for further diagnosis․ If the error code indicates a compressor issue, turn off the unit and seek professional help․ If the error code relates to the condenser, clean it and ensure proper airflow․ If the error code indicates a fan malfunction, check for blockages or worn parts․ If the error code relates to the defrost system, ensure the drain is clear and functioning properly․ If the error code persists, refer to the technical specifications for advanced troubleshooting․ If the error code indicates a communication error, check the wiring and connections between components․ If the error code relates to the user interface, reset the control panel or replace it if necessary․ If the error code indicates a software glitch, perform a factory reset or update the software․ If the error code persists, contact Sub-Zero’s technical support for assistance․ If the error code is not resolving, consider replacing the faulty module or component․ If the error code indicates a safety issue, turn off the appliance and contact a technician immediately․ If the error code relates to the door seals, check for proper alignment and replace if necessary․ If the error code indicates a leak, inspect the water supply lines and connections․ If the error code relates to the ice maker, refer to the ice maker troubleshooting guide․ If the error code persists after replacing parts, ensure all connections are secure and functioning correctly․ If the error code indicates a system failure, contact a certified technician for professional diagnosis and repair․ If the error code relates to the electrical system, check for loose connections or damaged wiring․ If the error code persists, refer to the service manual’s wiring diagrams for further guidance․ If the error code indicates a compressor issue, contact a technician to avoid further damage․ If the error code relates to the condenser, clean it and ensure proper airflow․ If the error code persists, refer to the manual’s maintenance section for routine care tips․ If the error code indicates a temperature issue, check the sensor calibration and ensure accurate readings․ If the error code relates to the evaporator, ensure proper airflow and check for blockages․ If the error code persists, contact a certified technician for professional assistance․ If the error code indicates a communication error, check the wiring and connections between components․ If the error code relates to the user interface, reset the control panel or replace it if necessary․ If the error code indicates a software glitch, perform a factory reset or update the software․ If the error code persists, contact Sub-Zero’s technical support for assistance․ If the error code is not resolving, consider replacing the faulty module or component․ If the error code indicates a safety issue, turn off the appliance and contact a technician immediately․ If the error code relates to the door seals, check for proper alignment and replace if necessary․ If the error code indicates a leak, inspect the water supply lines and connections․ If the error code relates to the ice maker, refer to the ice maker troubleshooting guide․ If the error code persists after replacing parts, ensure all connections are secure and functioning correctly․ If the error code indicates a system failure, contact a certified technician for professional diagnosis and repair․ If the error code relates to the electrical system, check for loose connections or damaged wiring․ If the error code persists, refer to the service manual’s wiring diagrams for further guidance․ If the error code indicates a compressor issue, contact a technician to avoid further damage; If the error code relates to the condenser, clean it and ensure proper airflow․ If the error code persists, refer to the manual’s maintenance section for routine care tips․ If the error code indicates a temperature issue, check the sensor calibration and ensure accurate readings․ If the error code relates to the evaporator, ensure proper airflow and check for blockages․ If the error code persists, contact a certified technician for professional assistance․ If the error code indicates a communication error, check the wiring and connections between components․ If the error code relates to the user interface, reset the control panel or replace it if necessary․ If the error code indicates a software glitch, perform a factory reset or update the software․ If the error code persists, contact Sub-Zero’s technical support for assistance․ If the error code is not resolving, consider replacing the faulty module or component․ If the error code indicates a safety issue, turn off the appliance and contact a technician immediately․ If the error code relates to the door seals, check for proper alignment and replace if necessary․ If the error code indicates a leak, inspect the water supply lines and connections․ If the error code relates to the ice maker, refer to the ice maker troubleshooting guide․ If the error code persists after replacing parts, ensure all connections are secure and functioning correctly․ If the error code indicates a system failure, contact a certified technician for professional diagnosis and repair․ If the error code relates to the electrical system, check for loose connections or damaged wiring․ If the error code persists, refer to the service manual’s wiring diagrams for further guidance․ If the error code indicates a compressor issue, contact a technician to avoid further damage․ If the error code relates to the condenser, clean it and ensure proper airflow․ If the error code persists, refer to the manual’s maintenance section for routine care tips․ If the error code indicates a temperature issue, check the sensor calibration and ensure accurate readings․ If the error code relates to the evaporator, ensure proper airflow and check for blockages․ If the error code persists, contact a certified technician for professional assistance․ If the error code indicates a communication error, check the wiring and connections between components․ If the error code relates to the user interface, reset the control panel or replace it if necessary․ If the error code indicates a software glitch, perform a factory reset or update the software․ If the error code persists, contact Sub-Zero’s technical support for assistance․ If the error code is not resolving, consider replacing the faulty module or component․ If the error code indicates a safety issue, turn off the appliance and contact a technician immediately․ If the error code relates to the door seals, check for proper alignment and replace if necessary․ If the error code indicates a leak, inspect the water supply lines and connections․ If the error code relates to the ice maker, refer to the ice maker troubleshooting guide․ If the error code persists after replacing parts, ensure all connections are secure and functioning correctly․ If the error code indicates a system failure, contact a certified technician for professional diagnosis and repair․ If the error code relates to the electrical system, check for loose connections or damaged wiring․ If the error code persists, refer to the service
Maintenance and Upkeep
Regular maintenance is essential for optimal performance․ Clean the condenser periodically, inspect door seals for tightness, and follow the routine service schedule outlined in the manual․ Always ensure proper airflow around the unit and check for any blockages․ Additionally, verify that all electrical connections are secure and functioning correctly․ If you notice any unusual noises or temperature fluctuations, address them promptly to prevent further issues․ Regular upkeep helps extend the appliance’s lifespan and maintains energy efficiency․ If unsure about any maintenance tasks, consult the service manual or contact a certified technician for professional assistance․ Proper care ensures your Sub-Zero 650 operates effectively and reliably over the years․
Leave a Reply
You must be logged in to post a comment.